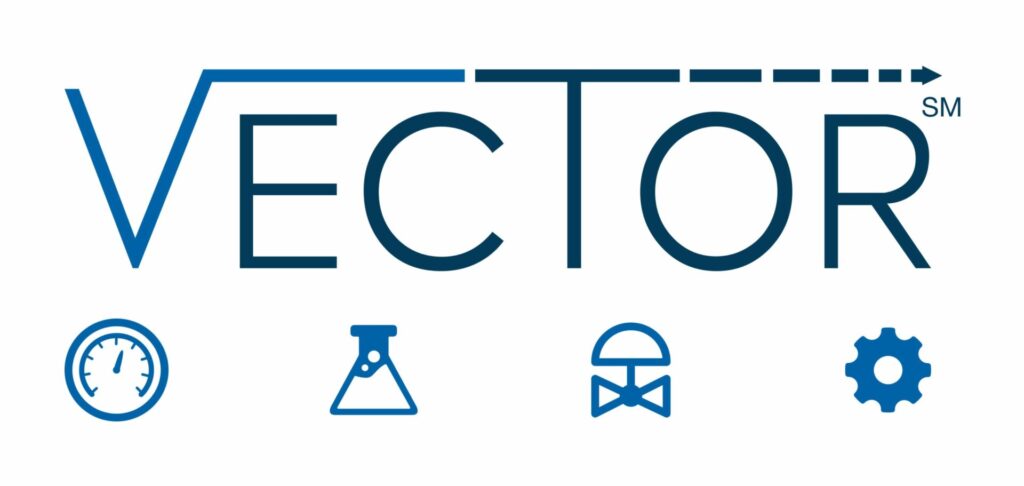
Vector Controls and Automation Group (CAG) was established in 2013. The Vector team has extensive experience and expertise in collaboration with leading industrial manufacturers, propelling the consolidated entity to the status of a comprehensive solutions and service provider. Vector’s headquarters is situated in Pearland, Texas, just south of Houston, and the organization maintains an additional five branches dedicated to serving customers on a local level. Vector extends its offerings of products, tailored engineering solutions, technical training and service to clients spanning various industries across the Southern and Midwestern states.
What is the unique value you bring to your customers through your products and services?
Vector CAG is a leading representative specializing in providing engineered solutions for instrumentation applications, complete analyzer solutions (encompassing engineering, design and integration), valve solutions (automation and service) and a comprehensive training program offered through Vector University.
Can you describe the steps you take to build and maintain your relationship with customers?
Our customer relationships begin from the initial interaction with Vector. We boast a dedicated team that includes Application Engineers, an extensive network of Subject Matter Experts, Customer Support Personnel, Project Managers, Service Coordinators, Service Engineers, Field Account Managers, and the added convenience of Online Live Chat, all staffed with experts equipped to address any issue, whether it’s straightforward or complex. Our unwavering commitment is to provide unparalleled customer service, delivering a comprehensive Vector 360 Experience.
Provide a brief overview of what your portfolio includes.
Vector CAG has a complete portfolio of process control instrumentation through Endress+Hauser and complementary product lines. In addition, our product portfolio includes a wide selection of offerings in Fire and Gas Detection, Heat Trace Solutions, Automation, Valves, and an extensive range of Analyzers, inclusive of engineering, design, integration, and maintenance services.
What is something you are continually improving on to maintain customer satisfaction?
Vector CAG has established an internal Process Excellence Committee (PEC) aimed at taking a proactive approach to address each business unit’s operations. This involves assessing existing processes, identifying inefficiencies or challenges, formulating new process models, executing these changes and subsequently assessing their impact to ensure visible benefits for both our customers and manufacturing partners. The PIC comprises representatives from various stakeholders and business units across the company, ensuring comprehensive representation and diverse perspectives are valued.
What do you enjoy most about being a partner with Endress+Hauser?
Vector CAG values its partnership with Endress+Hauser for many reasons, primarily the exceptional people within their organization. While outstanding products and solutions are important, their significance is truly realized when they are backed by dedicated individuals who take ownership of their processes and embrace a collaborative partnership approach. Endress+Hauser’s unwavering customer-centricity extends both internally and externally, with their work revolving around enhancing our customer relationships and setting the benchmark for excellence. In moments of truth, Endress+Hauser is there.
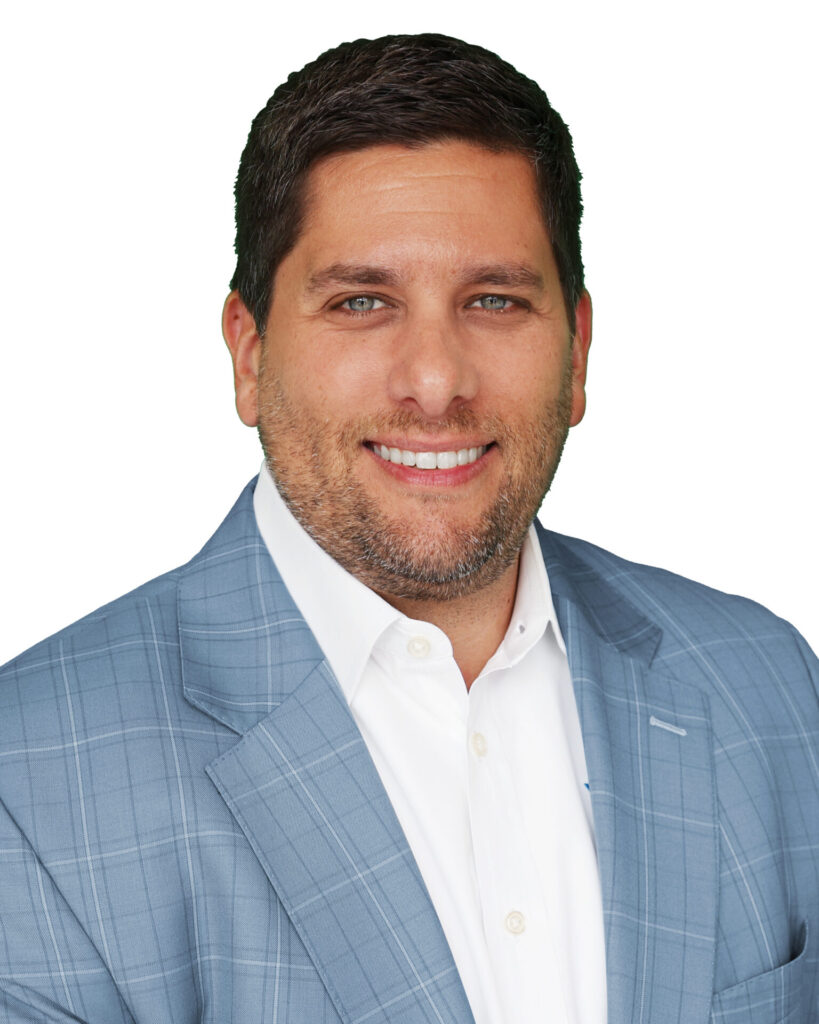
“We aim for our customers to recognize our unwavering commitment to their success and understand that, in our own modest way, we contribute to addressing some of our country’s most significant challenges through our collaboration with them. Whether it’s advancing clean and abundant energy, ensuring safe and accessible food supplies, promoting clean air and water, driving technological innovations, supporting space exploration or aiding in the development of life-saving pharmaceuticals, Vector CAG is there to enhance their businesses and play a role in improving the quality of life for both current and future generations.”
Jared Boudreaux, President, Vector Controls and Automation Group
Comments